5 Key Factors to Consider When Renting a PortaPack Generator
In the world of refrigerated transport and storage, maintaining consistent power is non-negotiable. A single power outage can lead to spoiled goods, missed deliveries, and significant financial losses. Renting a PortaPack generator is an ideal solution to ensure your reefer (refrigerated) generators stay operational, even during emergencies or planned downtime. Designed for portability and reliability, PortaPack generators are perfect for the unique demands of the cold chain industry. Here are five critical factors to consider before renting one.
1. Power Requirements for Refrigerated Loads
Reefer generators have specific power demands to keep refrigerated containers, trucks, or storage units at optimal temperatures. When renting a PortaPack generator, calculate the total power required, factoring in the cooling units’ starting and running loads. PortaPack generators are designed to handle high-demand loads, ensuring your perishables remain at the right temperature without interruption. Be sure to communicate the specific wattage needs for your reefer units to ensure you rent a generator with the right capacity. If you're unsure of the wattage you need, we can help guide you.
2. Portability for On-the-Go Applications
Cold chain logistics often require mobility, especially for businesses transporting goods across regions or managing temporary storage sites. PortaPack generators are built for portability, making them easy to transport and set up at loading docks, warehouses, or on the road. Their compact design ensures they can be seamlessly integrated with reefer systems, providing reliable power wherever you need it. Whether you’re powering a single refrigerated container or multiple units, the PortaPack's mobility is a key advantage.
3. Fuel Efficiency for Cost-Effective Cooling
Fuel efficiency is a critical consideration for refrigerated operations, where generators often need to run continuously for extended periods. PortaPack generators typically run on diesel, offering a balance of cost-efficiency and reliability. With optimized fuel consumption, they ensure that your reefer units remain powered without driving up operational costs. Be sure to choose a generator with a fuel tank capacity and runtime that matches the duration of your transport or storage needs.
4. Reliability in Critical Situations
In the cold chain industry, downtime is not an option. PortaPack generators are designed for rugged use and consistent performance, ensuring that your refrigerated goods are never at risk of spoiling. When renting, confirm that the generator provider offers well-maintained equipment, technical support, and fast response times for troubleshooting. Look for rental agreements that include routine maintenance, replacement options, and 24/7 customer support to safeguard your operations.
5. Noise and Compliance
Noise can be a concern when operating generators near residential areas, urban warehouses, or at ports. PortaPack generators are equipped with sound attenuation features, ensuring quiet operation without compromising power output. Additionally, check that the generator meets emissions and safety standards, as compliance is often required for refrigerated transport in certain regions or facilities.
Final Thoughts
For businesses relying on refrigerated generators, renting a PortaPack generator is a smart, flexible solution to keep goods at the right temperature, no matter the circumstances. By assessing power requirements, taking advantage of PortaPack’s portability, prioritizing fuel efficiency, and ensuring reliability, you can protect your cold chain operations and avoid costly disruptions.
Don’t let power outages put your goods at risk. Rent a PortaPack generator today and keep your reefer units running smoothly!
Designing Sound Attenuation for Reefer Generators at Power Pool Plus
Reefer generators are essential for keeping perishable goods at optimal temperatures during transit, but the noise they produce can present challenges—from disturbing operators and the environment to failing noise regulations. At Power Pool Plus, we specialize in designing effective sound attenuation systems that balance performance with quiet operation, using advanced acoustics and smart engineering.
The Challenge of Reefer Generator Noise
Reefer generators generate noise from several sources—engine combustion, exhaust discharge, and the mechanical vibrations of moving parts. If not addressed, this noise can disrupt workers, disturb nearby areas, and create compliance issues with environmental and workplace regulations. Identifying the sources and frequencies of these sounds is the first step toward crafting effective sound control solutions.
Core Principles of Sound Attenuation
Our sound attenuation solutions focus on key methods to reduce noise transmission:
- Damping: This method involves using materials to reduce vibrations at the source, minimizing noise before it spreads.
- Isolation: By physically separating vibrating components from the generator frame, we limit noise transmission to the surrounding environment.
A Multi-Layered Approach to Noise Control
Building world-class sound attenuation solutions involves several key elements:
- Material Selection Matters
We choose high-performance materials like acoustic foam, fiberglass, and composite barriers. These materials offer superior sound absorption while being tough enough to withstand extreme temperatures, moisture, and the operational demands of reefer generators. The materials we use not only block noise but also ensure long-term durability.
- Custom Engineered Enclosures
Our custom-built enclosures are designed to trap and absorb noise while ensuring adequate ventilation to prevent overheating. These enclosures are lined with acoustic material to dampen noise, and their layouts are precisely engineered to fit the unique configuration of each generator.
- Vibration Control Solutions
Reducing vibrations at the source is critical to lowering noise levels. We integrate anti-vibration mounts, pads, and shock absorbers to reduce mechanical resonance and stop noise from radiating through the structure. This minimizes operational disruptions and ensures quiet performance.
Achieving the Perfect Balance: Quiet Power, Reliable Performance
At Power Pool Plus, we understand that reliable performance and quiet operation go hand-in-hand. Our sound attenuation enclosures help businesses meet noise regulations while maintaining efficiency. With precision-engineered enclosures, advanced materials, and vibration control solutions, we make sure reefer generators operate harmoniously, minimizing their noise footprint without sacrificing power.
Our goal? To deliver the quietest, most reliable reefer generators on the market—because powerful solutions shouldn’t have to be loud.
Refurbishing Power Pack Reefer Generators: How to Save Money and Time
In the world of refrigerated transport and cold-chain logistics, power pack reefer generators are vital. They ensure the integrity of the cold chain, protecting perishable goods and refrigerated freight during transit.
However, these refrigerated generators require regular maintenance. Without it, their efficiency can drop, leading to costly breakdowns and cargo spoilage.
This article will guide you through the best practices for maintaining and refurbishing your power pack reefer generators. It aims to help you extend their lifespan, reduce downtime, and save money on repairs and replacements.
Stay tuned to learn how to keep your refrigerated transport running smoothly and efficiently.
Understanding Power Pack Reefer Generators
Power pack reefer generators play a crucial role in refrigerated transport. They provide the energy needed to maintain the temperature inside refrigerated containers.
These power pack generators are designed to withstand harsh conditions. They are robust, reliable, and built to last. However, like any mechanical equipment, they require regular care to perform at their best.
Understanding how these generators work is the first step towards effective maintenance. They operate on a simple principle: converting fuel into electricity to power the refrigeration unit.
Key components of a power pack reefer generator include:
- The engine
- The alternator
- The fuel system
- The cooling system
- The control panel
Knowing these components and their functions can help you identify potential issues early. This knowledge is essential for effective maintenance and refurbishment.
The Importance of Regular Maintenance
Regular maintenance of power pack reefer generators is vital. It ensures the reliability and efficiency of refrigerated transport.
Without proper care, these generators can break down. This can lead to costly repairs and downtime. Worse, it can compromise the integrity of the cold chain, leading to spoilage of perishable goods.
Regular maintenance can prevent these issues. It can extend the lifespan of your generators, reduce downtime, and save money on repairs and replacements.
Here are some key benefits of regular maintenance:
- Ensures the efficiency and reliability of refrigerated transport
- Prevents costly breakdowns and cargo spoilage
- Extends the lifespan of the generator
- Saves money on repairs and replacements
In short, regular maintenance is an investment. It pays off in the long run by ensuring the smooth operation of your refrigerated transport.
Step-by-Step Maintenance Guide
Maintaining your power pack reefer generator doesn't have to be a daunting task. With a systematic approach, you can ensure its optimal performance.
First, create a maintenance schedule. This should include daily, weekly, monthly, and annual checks.
Here are some key steps to include in your maintenance routine:
- Check the fuel level and refill if necessary.
- Inspect the generator for any visible damage or leaks.
- Clean the generator and its components to remove dust and debris.
- Check the battery and replace it if it's not holding a charge.
- Inspect the insulation and airflow system for any issues.
- Check the refrigerant level and refill if necessary.
- Inspect the electrical connections and tighten any loose ones.
- Perform a load test to ensure the generator is working efficiently.
Remember, safety first. Always turn off the generator and disconnect it from the power source before performing any maintenance tasks.
Also, keep a record of all maintenance activities. This can help you identify recurring issues and plan for future maintenance.
Lastly, don't hesitate to call in a professional if you encounter any issues beyond your expertise. Regular maintenance can go a long way in ensuring the longevity and efficiency of your power pack reefer generator.
Identifying Common Issues and Troubleshooting
Power pack reefer generators, like any mechanical equipment, can develop issues over time. Being able to identify these issues early can save you time and money.
Here are some common issues you might encounter:
- The generator doesn't start: This could be due to a dead battery, a faulty starter motor, or a problem with the fuel system.
- The generator is overheating: This could be due to a lack of coolant, a blocked radiator, or a faulty thermostat.
- The generator is making unusual noises: This could indicate a problem with the engine, such as worn-out bearings or a damaged piston.
- The generator is using too much fuel: This could be due to a dirty air filter, a problem with the fuel injection system, or a lack of regular maintenance.
If you encounter any of these issues, start by checking the most common causes. For example, if the generator doesn't start, check the battery and the fuel system first.
However, if you can't identify or fix the issue, it's best to call in a professional. Trying to fix a complex issue without the right skills or tools can cause more harm than good.
When to Refurbish Your Reefer Generator
Knowing when to refurbish your reefer generator is crucial. It can help you avoid costly breakdowns and extend the lifespan of your equipment.
One sign that your generator may need refurbishing is frequent breakdowns. If you're constantly having to repair your generator, it might be more cost-effective to refurbish it.
Another sign is decreased performance. If your generator is using more fuel than usual or struggling to maintain the right temperature, it might be time for a refurbishment.
Remember, regular maintenance can help you spot these signs early. It's always better to refurbish your generator before it breaks down completely.
The Refurbishment Process: Saving Money and Extending Lifespan
Refurbishing your power pack reefer generator can save you money in the long run. It can also extend the lifespan of your equipment, reducing the need for costly replacements.
The refurbishment process involves several steps. These include inspecting the generator, replacing worn-out parts, and testing the equipment to ensure it's working properly.
Here are the key steps in the refurbishment process:
- Inspection: The generator is thoroughly inspected for any signs of wear and tear.
- Replacement of Parts: Any worn-out or damaged parts are replaced with new ones.
- Testing: The refurbished generator is tested to ensure it's working properly.
Our Process:
- Complete removal of all interior components including end frame
- Container: New container was provided and fabricated to Power Pool Plus design specifications
- Engine: Overhauled in our shop with all new wear parts, cleaned and tested
- Radiator: Re-cored to provide better efficiency and cooling
- Re-coring is the process of re-fitting the inside coils with new components
- Radiators are a key component in Power Pack operation. Whenever possible Power Pool Plus will resource the best possible solution to ensure proper cooling capabilities that exceed customer requirements.
- Generator: Re-built and baked with new tropical coatings to protect the windings from excessive moisture
- Fuel Tank: Inspected for damage. Optional service, if necessary, to cut open for interior mechanical cleaning in the event of an excessive algae build-up scenario.
- Lighting: Increased number of fixtures and upgraded all lighting to high intensity, LED lamps. A critical feature to those that will be servicing the unit.
- End Frame: In this scenario we were able to save the end frame and integrated receptacle panel from the original unit for re-use. This helped us to save the customer $1000′s in replacement costs.
- Improvements: During this process we were also able to recommend to the customer specific areas where Power Pack performance could be enhanced.
- In this case, the original unit provided insufficient air flow for proper cooling and engine operation. The original container was entirely closed providing no access to service large components; such as, radiator, silencer, engine, or generator, without compromising the box through cutting, re-welding, and painting.
- Customer agreed to have us incorporate additional rain proof exhaust louvers and access doors per current Power Pool Plus design. This ensured easy accessibility for maintenance which will extend the service life of the machine.
- Cosmetic Improvement: Freshly painted both inside and out. It’s not just about looking good.
- Having a clean, freshly painted Power pack not only looks nice, but it ensures a solid base protection from the elements by mitigating the negative effects of rust and corrosion. o Interior painting provides extra bright visibility inside the machine which not only aids in maintenance service, but also helps to visually identify potential leaks
Conclusion: The Benefits of Maintaining and Refurbishing Your Power Pack
Regular maintenance and timely refurbishment of your power pack reefer generator are crucial. They ensure the efficiency, longevity, and reliability of your refrigerated transport.
In the end, these practices save you money and time. They also contribute to the integrity of the cold chain, ensuring the safe transport of perishable goods.
Prepare Your Reefer Containers for Hurricane Season with Power Pool Plus
As hurricane season approaches, ensuring that your reefer containers remain operational during storms is crucial for maintaining the integrity of your perishable cargo. At Power Pool Plus, we understand the importance of reliable power solutions for your refrigerated freight containers. Our Power Packs and PortaPacks are designed to keep your reefer containers powered and your goods safe, no matter the weather conditions.
A beautiful shot of lightning strike in the night sky over the city on a stormy night. Mystical cloudsA stunning view of a bustling cityscape at night, illuminated by the shimmering lights along the waterfront in AlkmaarHere are some essential tips to prepare your reefer containers for hurricane season:
1. Perform Regular Maintenance
Regular maintenance of your Power Packs and PortaPacks is key to ensuring they function optimally during a storm. Check for any signs of wear and tear, ensure fuel levels are adequate, and test the systems to make sure they are operating correctly. Preventive maintenance can help you avoid unexpected failures when you need power the most.
2. Secure Your Equipment
During a hurricane, high winds and flying debris can pose significant risks to your equipment. Secure your Power Packs and PortaPacks by anchoring them properly and protecting the cable ports with additional suitable covers. This will minimize the risk of damage and ensure that your power supply remains uninterrupted.
3. Have a Backup Plan
Despite the best preparations, sometimes things can still go wrong. Having a backup plan in place is essential. Consider having additional Power Packs or PortaPacks on standby, and ensure your team knows how to quickly navigate your freight yard and manage units if necessary. This redundancy can be a lifesaver during extended power outages.
4. Monitor Weather Conditions
Stay informed about upcoming weather conditions and be proactive in your preparations. If a hurricane is forecasted, ensure that all reefer containers are adequately powered and that your generators are in prime working condition. Early preparation can make all the difference in maintaining the integrity of your refrigerated goods.
5. Keep Emergency Contacts Handy
Have a list of emergency contacts readily available, including your generator service provider, local utility companies, and emergency services. Quick access to these contacts can expedite repairs and assistance in case of equipment failure during a storm.
6. Conduct Emergency Drills
Regularly conduct emergency drills with your team to ensure everyone knows their roles and responsibilities during a hurricane. Practicing these scenarios will help your team respond swiftly and efficiently, minimizing downtime and potential losses.
At Power Pool Plus, we are committed to providing robust and reliable power solutions for your reefer containers. Our Power Packs and PortaPacks are built to withstand harsh conditions and keep your operations running smoothly, even during a hurricane.
By following these tips and using our dependable power solutions, you can ensure that your reefer containers remain operational and your perishable goods stay protected throughout hurricane season.
Stay prepared and stay powered with Power Pool Plus.
For more information and expert advice, visit our website or contact our team today.
Global Food Waste Prevention: Innovations and Insights
Addressing the Food Waste Crisis
Food waste is a pressing global issue, with about a third of the food produced annually going to waste, according to the United Nations’ Food and Agriculture Organization. A recent study from the University of Michigan reveals that nearly half of this waste, approximately 620 million metric tons, could be eliminated by implementing fully refrigerated food supply chains worldwide.
Aaron Friedman-Heiman, a master’s student at the University of Michigan’s School for Environment and Sustainability and Ross School of Business, spearheaded this study. He highlights the enormous potential for reducing food loss and waste through supply-chain optimization. The study estimates that inadequate cold-chain infrastructure is a major contributor to global food loss, leading to significant greenhouse gas emissions.
Environmental Impact: Poor cold-chain infrastructure results in the emission of 1.8 billion tons of carbon dioxide equivalents, accounting for 28% of annual greenhouse gas emissions in the U.S. Therefore, improving warehousing and other aspects of the cold chain is crucial for minimizing food waste and mitigating its environmental impact.
The Importance of Cold-Chain Logistics in Food Preservation
Cold-chain logistics is vital in the food industry. It involves the transportation of temperature-sensitive goods in a temperature-controlled environment. This process ensures the freshness and safety of perishable goods, extending their shelf-life, and reducing the risk of spoilage and waste.
Global Food Waste: A Challenge and Opportunity
Global food waste has significant environmental, economic, and social implications. Yet, it also presents an opportunity. By improving cold-chain logistics, we can reduce food waste and its impacts, including:
- Increased greenhouse gas emissions
- Economic losses for producers and consumers
- Wasted resources used in food production
- Increased pressure on land and water resources
- Threats to food security and sustainable development
Advancements in Cold-Chain Technology
Cold-chain logistics technology has seen significant advancements in recent years. These improvements have the potential to revolutionize the way we handle perishable goods. From IoT devices to AI-powered analytics, these technologies are making cold-chain operations more efficient and reliable. They help maintain the quality of food products, reducing waste, and promoting sustainable living.
Refrigerated Transport and Its Impact
Refrigerated transport plays a crucial role in the cold-chain. It ensures that perishable goods are kept at the right temperature during transit, preserving their quality and safety. With advancements in refrigeration technology, transport vehicles can now maintain more consistent temperatures. This reduces the risk of spoilage and contributes to global food waste prevention.
The Role of Reefer Generators in Cold-Chain Efficiency
Refrigerated generators (aka reefers) are another key component of the cold-chain. They provide the power needed to keep refrigeration units running during transport. By improving the efficiency of these generators, we can reduce energy consumption and environmental impact. This also leads to cost savings, making cold-chain operations more sustainable and economically viable.
Resource Management for Sustainable Cold-Chain Operations
Effective resource management is key to sustainable cold-chain operations. It involves optimizing the use of energy, equipment, and manpower to reduce waste and improve efficiency. By adopting best practices in resource management, businesses can reduce their environmental footprint and achieve significant cost savings, making their operations more sustainable and profitable.
Implementing IoT and AI for Smarter Logistics
The use of IoT and AI in cold-chain logistics is a game-changer. These technologies enable real-time monitoring and predictive analytics, enhancing the efficiency and reliability of operations. With IoT devices, businesses can track the condition of their goods in real-time. AI, on the other hand, can analyze this data to predict potential issues and suggest preventive measures.
Real-Time Data Tracking and Its Benefits
Real-time data tracking provides businesses with up-to-the-minute information about their operations, enabling them to make informed decisions. By tracking data in real-time, businesses can quickly identify and address issues. This reduces the risk of spoilage and waste, contributing to global food waste prevention and sustainable living.
Overcoming Cold-Chain Logistics Challenges
Despite advancements in cold-chain logistics technology, several challenges remain. These include maintaining temperature control, ensuring energy efficiency, and addressing the last-mile delivery problem. However, with continuous innovation and collaboration among stakeholders, these challenges can be overcome, paving the way for more efficient and sustainable cold-chain operations.
Addressing the Last-Mile Delivery Problem
The last-mile delivery problem involves maintaining the quality and safety of perishable goods during their final journey to the consumer. Innovative solutions, such as mobile cold storage and smart containers, are being developed to address this issue. These technologies help ensure that perishable goods reach consumers in optimal condition, reducing food waste and promoting sustainable living.
Case Studies: Success Stories in Cold-Chain Logistics
Several companies have successfully implemented advanced cold-chain logistics technology to reduce food waste. For instance, some have leveraged IoT and AI to enhance their operations, resulting in improved efficiency and reduced spoilage. Others have used refrigerated transport generators to maintain optimal temperatures during transport. These success stories serve as a testament to the potential of cold-chain logistics technology in addressing global food waste.
The Future of Cold-Chain Logistics Technology
The future of cold-chain logistics technology looks promising. With continuous innovation and advancements in technology, the sector is poised to become more efficient and sustainable. The integration of IoT, AI, and blockchain technology is expected to revolutionize the industry, offering real-time tracking, predictive analytics, and enhanced traceability.
Moreover, the use of sensor technology and smart containers could further improve the quality and safety of perishable goods. These advancements will not only reduce food waste but also contribute to cost savings and improved food security.
Conclusion: The Role of Stakeholders in Reducing Food Waste
The fight against global food waste is a collective effort. Stakeholders across the supply chain, from farmers to retailers, have a crucial role to play. By adopting advanced cold-chain logistics technology and sustainable practices, they can significantly reduce food waste and contribute to a more sustainable future.
Moreover, consumers, policymakers, and technology providers also have a part to play. Through education, regulation, and continuous innovation, we can make a significant impact on global food waste prevention.al food waste prevention.
Custom Generator Solutions for Refrigerated Cargo
As the demand for transporting temperature-sensitive goods continues to rise, the importance of reliable refrigerated transport (reefer) solutions has never been more critical. From pharmaceuticals to perishable food items, ensuring these goods reach their destination in pristine condition is a top priority for shipping companies. Custom built power generation solutions for refrigerated transport are key to meeting these stringent requirements. Here’s a look at how custom reefer genset solutions are powering the cold chain logistics industry.
Understanding Reefer Gensets
Reefer gensets, or refrigerated generators, are specialized power generation units designed to maintain the necessary temperature controls within refrigerated containers during transport. These units are essential for the movement of refrigerated cargo, particularly when transported via trucks, trains, or ships where access to a stable power source is not always guaranteed.
Why Custom Solutions?
Every refrigerated transport operation has its unique set of challenges. Factors such as the type of goods being transported, the duration of the shipment, and the specific temperature requirements all necessitate tailored power solutions. Custom power generation solutions for refrigerated transport are designed to meet the precise needs of each shipment, ensuring optimal performance and reliability.
Custom Reefer Genset Solutions
Custom reefer genset solutions take into account the cargo's size, weight, temperature sensitivity, and the journey's length to ensure that the goods remain at the right temperature throughout transit. By customizing the power generation units, companies can avoid the one-size-fits-all approach, which may not be suitable for all types of refrigerated cargo.
Benefits of Customization
The benefits of opting for custom reefer genset solutions include increased efficiency, reduced operational costs, and enhanced protection for sensitive goods. Customization can lead to gensets that are more fuel-efficient, have better temperature control, and are designed to fit perfectly with the transport containers in use. This tailored approach can also extend the lifespan of the gensets, as they are built to withstand the specific conditions they will face.
Innovation in Refrigerated Cargo Power
The refrigerated cargo shipping industry continues to innovate, with new technologies improving the efficiency and sustainability of reefer gensets. Companies now offer gensets with smart monitoring systems that allow for real-time tracking and adjustments to temperature settings. These advancements ensure that custom reefer genset solutions are not only reliable but also at the forefront of technology.
Partnering with Experts
When it comes to acquiring custom reefer genset solutions, partnering with an experienced manufacturer like Power Pool Plus is crucial. Our team of experts can assess your specific requirements and design a power generation solution that aligns with your operational needs. With the right partnership, you can secure the robust and reliable reefer generators necessary for successful refrigerated cargo shipping.
Custom built power generation solutions are integral to the success of refrigerated transport. With the right genset in place, companies can ensure that their temperature-sensitive goods are transported safely and efficiently, maintaining quality and freshness upon arrival. As the industry evolves, Power Pool Plus's custom solutions will continue to play a pivotal role in the advancement of refrigerated cargo power.
Put Your Engine to Work – Repurpose A Refurbished Power Plant in a New Power Pack!
Drawing from our extensive experience of refurbishing used Power Packs, the team at Power Pool Plus is proud to introduce a new option for customers in urgent need of a power solution. Power Pool Plus is now offering complete Power Pack builds around existing preowned power plants! Due to global supply chain backup, the lead time for new engine skid packages is now up to over 40 weeks long, a time frame incompatible with the demands of many operations in need of mobile energy. Couple this with trending inflation of material pricing and the scarcity of available rental units, the landscape of available energy solutions is sparse. If your organization is able to source a refurbished engine from its current Power Pack inventory, our expert team can construct an entirely new enclosure around it, putting it to work in record time compared to the wait for an entirely new unit. If you don’t happen to have a spare engine lying around, our team is able to provide a variety of refurbished motors to fit your needs. This process is not only quicker, but more cost effective for consumers in dire need of a power solution. We are able to utilize a variety of engine makes and sizes to create a custom build tailored to your operation!
Proudly Made in the United States of America!
Power Pool Plus is proud to manufacture the entirety of our product line in the United States of America. All of our Power Packs and PortaPacks™ are built from the ground up in our Greenwood, South Carolina Manufacturing Headquarters, creating over 20 new jobs for the local economy. With most companies choosing to offshore production over the past few decades, we are especially proud to double down on local investment by manufacturing our products domestically and employing American workers. In addition to our production team, our entire sales and service staff are based out of New Jersey and South Carolina. Whether you’re looking to purchase or rent on of our standard units or have a custom-built power supply created specifically to fit the needs of your operation, you can be sure that highly skilled and dedicated American workers power the process from beginning to end. We also encourage current reefer genset owners to take advantage of our re-manufacturing services to breathe new life into their units. We'll be glad to work on them even if they were not originally manufactured by us! We invite you to explore our entire product line!
Know when to replace your power cables
Check your power cables for safety and functionality
Without quality power cables to transfer electricity from the power pack generator to reefer racks or remote receptacle trees, keeping a reefer yard filled with refrigerated containers would be impossible.
Yet even the best-made cables require proper maintenance to ensure functionality and worker safety.
The ground cabling we use is dual-jacketed to protect the inner copper strands from damage. Yet, the constant dragging of cables across asphalt and gravel yards can take its toll.
Using color-contrasting layers provides a visual indicator. For example, when the outer jacket is worn through, cut, or scraped, the inner jacket reveals a distinctly white visual warning that it may be time to replace the cable.
This visual awareness provides easy identification of abrasion before reaching the copper stranding to ensure the safety of the operators.
See the image below provided by our friends at Trystar cable, which highlights the dual-jacket layers.
- Outer Jacket
- Inner Jacket
- Copper strands
A best practice when handling ground cables is to pick them up and move them into position to avoid unnecessary scuffs. Protect them from moving vehicle traffic, do not allow them to lay in pooling water, and inspect them frequently for damage.
Get a quote today, on your next Purpose-Built Power Pack.
Ted Shelson
VP Marketing
Power Pool Plus
How we're meeting today's supply chain challenges
An unprecedented challenge.
COVID shutdowns and lost labor time, shipping delays, crippling storms, and raw material shortages - Nearly all suppliers and end-users are experiencing challenges due to the inability to secure the parts and materials needed for timely production.
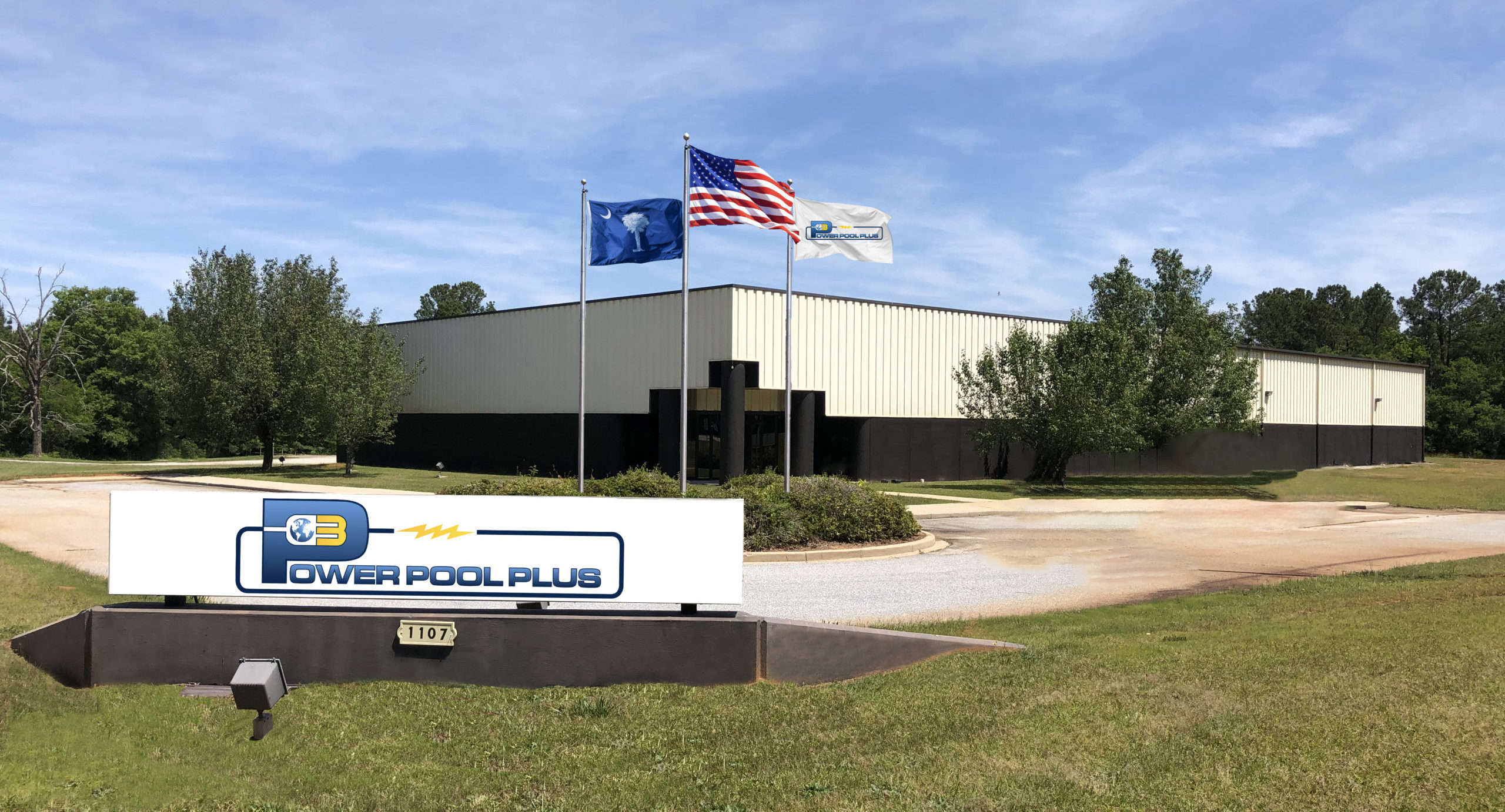
Power Pool Plus is no exception.
Even with the increased manufacturing capacity from our newly opened Greenwood, South Carolina plant, which affords us an additional 30,000sqft on 12+ acres of manufacturing space, delays in receiving raw materials for production prove problematic and negate any impact from this infrastructure investment.
For example, steel and electrical cable, two of the most used materials in our Power Packs, usually promised from our vendors in a few days, is now turning into 6-8 weeks or more. Our challenges are their challenges, as they count on commitments from their suppliers to turn products. It’s a vicious cycle.
According to a recent Wall Street Journal Report, up to 40 vessels anchored off Southern California ports had been waiting for dock space, which has since ebbed to around 17 earlier this week. While that is still too large a number, the backlog continues to shrink as ports and trucking catch up with the increased volumes.
But still, we are finding various steel products disappearing off our vendors’ shelves. And the availability of 20 and 40-ft high cube containers is also difficult to find at once typical prices. We continue to order in higher quantities than usual to stay ahead, so we have inventory to keep up with the demand.
While inflation has primarily been kept in check, there is talk about possible increases later in the year.
The good news is (there's always some good news),
as the world awakens from its COVID-induced sleep, it is clear that the demand for goods is strong. Consumers are looking to buy, and industries are ready to make investments to meet the demand. Refrigerated transport is no exception. As the demand for fresh produce increases, the need for power at ports to manage reefer throughput will remain high.
Our power packs are needed, orders are up, and accordingly, we have made investments in our production facilities to stay ahead.
So be patient. These delays will pass, and a sense of normalcy will resume. Until then, please know that all of us at Power Pool Plus are working hard to provide you with the finest Purpose-Built Reefer Power Genset on the market while remaining at a reasonable price to help your operation succeed.
Suppose your reefer management team is looking to increase productivity this year with new Power Pool Plus power packs. In that case, we highly suggest placing orders as soon as possible to minimize potential delays and expected increases in material costs.
Get a quote today, on your next Purpose-Built Power Pack.
Ted Shelson
VP Marketing
Power Pool Plus